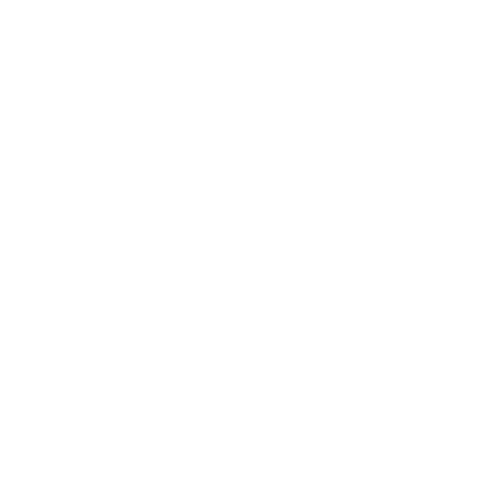
摘要
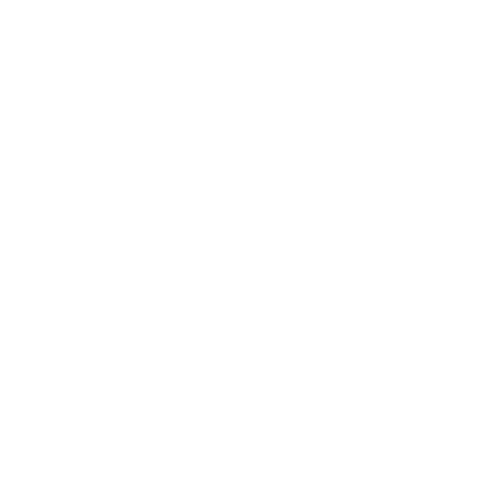
三球销式等速万向节因具有承载能力强、效率高、可靠性好等优势,是汽车驱动轴总成中应用最为广泛的万向节。随着对传动系统的可靠性以及NVH要求的提高,三球销式等速万向节由球环和滚道之间的摩擦引起的振动、噪声等问题日益突出。这些震动和噪音问题可通过降低驱动轴轴向派生力来解决,本文针对如何降低驱动轴轴向派生力提出了分析方法和解决措施,提升了万向节的性能。
【关键词】三球销式等速万向节,轴向派生力
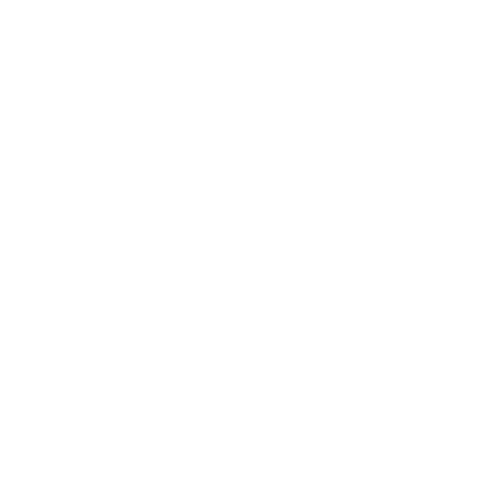
1.引言
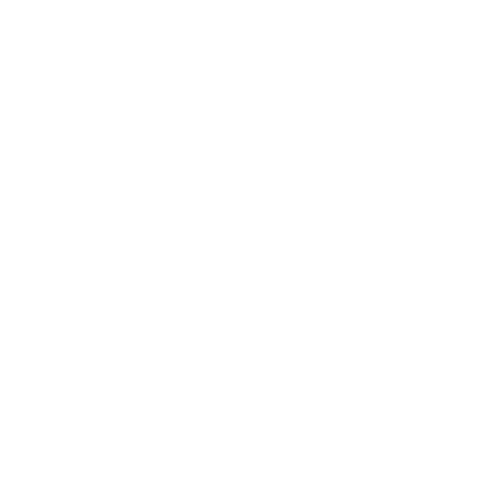
为了满足汽车以较高速度行驶时,驱动轴能稳定可靠的进行动力输出、吸收独立悬架跳动引起轴向位移差、驱动轴外端大转角等要求,目前广泛使用的等速万向节驱动轴总成,通常采用分段式(两段或三段),分段式结构可以有效减小传动过程中的滑移力、噪声及振动。
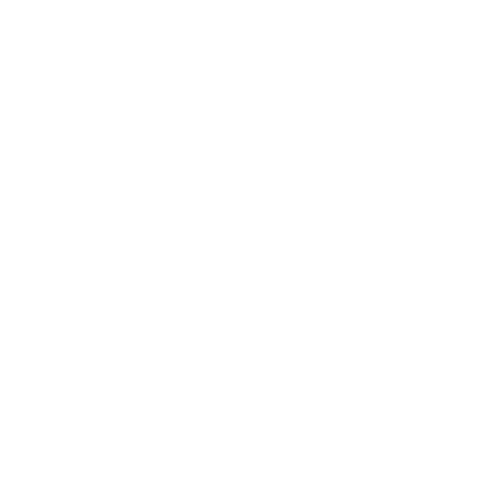
2.驱动轴常见结构
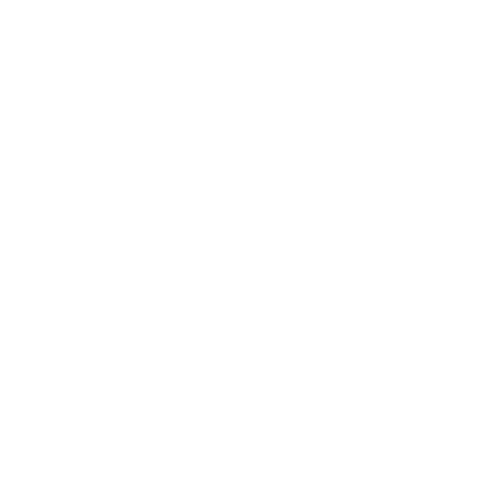
驱动轴系统主要由3个部分组成:(1)与车轮端相连的固定式万向节;(2)可轴向滑移式万向节,与变速器的差速器相连;(3)驱动轴,位于固定节和移动节之间,其中三销轴式等速万向节比较常见。结构如下图1-1
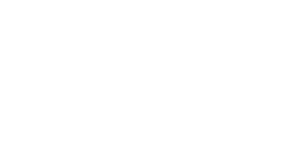
其中星形套、钟形壳与保持架通过两个球面副配合装配在一起,两个球面副的球心为等速节传动中心,星形套外球面及钟形壳的球面上分别有六个钢球沟道,该结构的特点是万向节在任意夹角下传动时,钢球始终位于输入轴与输出轴的角平分面上。三销架上均匀的分布着三个销轴,相互之间的夹角为2/3π。同时,球环通过滚针与销轴相连,球环可以沿着销轴的轴线移动,也可以绕着销轴轴线转动。三柱槽壳内有三条沿着槽壳轴线方向的滑槽,三个球环分别嵌入三条滑槽内,并且可以沿着滑槽轴向滑移,球环与滑槽间的配合间隙很小,以确保传动的平稳性。当三柱槽壳与三销架间存在一定摆角,并且在三柱槽壳上施加一定的扭矩后,通过球环把扭矩传递给三销架,带动三销架转动,在转动的过程中,三销架会沿着三柱槽壳轴线滑进与滑出,以补偿万向节轴向长度的变化。由于万向节内部的摩擦特性和运动特性,三销轴万向节在工作过程中会产生一个周期性的轴向力,称为轴向派生力。当不存在外部轴向位移激励时,在给定输入转速和负载转矩下,由移动节产生的沿其输入轴轴线方向的力,见图 1-2。图中,M1为万向节的负载转矩,Md为万向节的驱动转矩,nd为万向节的输入转速。对于三球销式等速万向节,其轴向派生力是由它的3个球环沿各自滚道的周期性往复运动产生的摩擦力叠加而成。因此,三球销式等速万向节的轴向派生力的波动频率通常为万向节输入转频的3阶[1,3]。万向节工作过程中产生的轴向派生力会给机械系统施加振动激励,引起汽车振动和噪声问题。万向节的轴向派生力会给汽车施加横向交变载荷,引起汽车的横向振动。因此,万向节的轴向派生力对汽车NVH性能有不良的影响。由于人体对于水平方向的中低频振动较为敏感,因而当车速较低时,万向节的对汽车NVH性能的影响尤为明显。当车辆突然加速时,施加在万向节上的转矩会急剧增大,滚道和球环之间的摩擦力也相应地急剧增大,导致万向节的轴向派生力也急剧增大,加剧了汽车的横向抖动,恶化了汽车的乘坐舒适性。因此,在三球销式等速万向节的设计过程中,应尽可能减小轴向派生力。
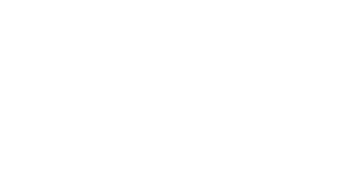
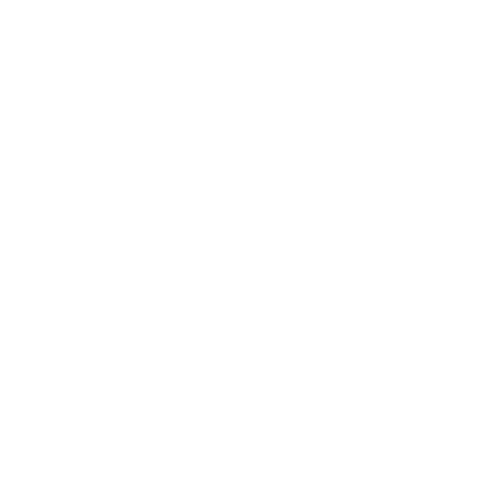
3.轴向派生力影响因素
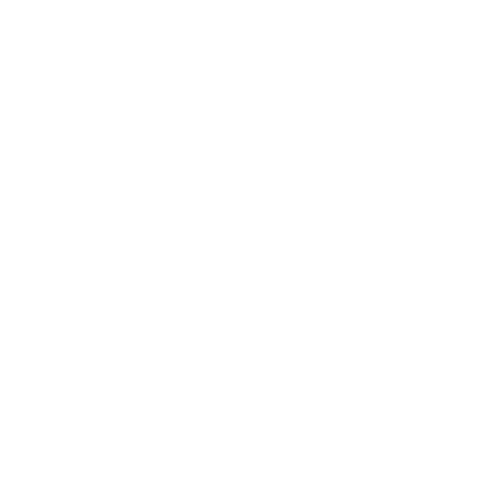
根据文献[4,7]影响轴向派生力的主要因素有三销节的节圆半径(即三销节中心到滚道中心线的距离)、摩擦系数、接触参数、驱动轴的工作角度、负载扭矩和转速。其中节圆半径是影响轴向派生力的尺寸参数。节圆半径的精度较高(公差一般为0.05mm),其对轴向派生力的影响较小。在不同工况(工作角度、扭矩和转速)下,节圆半径可视为常数。而在不同工况下,由于三销节内部接触状态和摩擦状态的变化,接触副的接触参数和摩擦参数(如接触刚度、力指数、静摩擦系数和动摩擦系数)对轴向派生力影响很大。驱动轴系统的工作角度、转速、负载转矩及万向节内部接触对的摩擦系数对轴向派生力都有很大影响。特别是在高工作角度、高转动扭矩、低转速时,驱动轴系统会产生较高的轴向派生力。其中工作角度主要由动总在车身上的布置位置和球道轨道尺寸决定,转速、转动扭矩一般由发动机和变速箱工况确定。某主机厂新车型开发初期,轴向派生力在转矩1400N/m和6°转角时达到85.6N,超过技术要求(小于60N),通过台架试验排查分析,轴向派生力过大主要来源于万向节的内部零件摩擦力过大,而摩擦力主要来源于以下三个方面:(一)滚针轴承内部的滚动摩擦力,其轴向分力为F1。一般采用转动性更好的滚针轴承来降低滚动摩擦力,从而降低F1。(二)球环与滑槽间的摩擦力:滚针轴承外圈外表面与三柱槽壳体滚道之间的滚动摩擦力,其轴向分力为F2。F2为滚道与滚针轴承外球环之间的法向力Q产生的摩擦力,AAR节型的外球环与滚道始终保持平行状态,当半轴运转时,外球环在滚道内的运动不会因三销架和三柱槽壳之间出现的摆角而发生变化。在对三柱槽壳施加载荷M后,由于滚道的圆弧中心高R不变,理论上Q=M/3R,故滚道法向力Q不变,F2=u滚动 × Q,可以通过降低滚动摩擦系数u来减小F2,如提高球环和滚道表面粗糙度精度、使用低摩擦系数油脂等方案。但球环和滚道由于制造精度等因素,实绩两者之间存在一定的间隙,故球笼在转动/摆动过程中,球环相对滚道还是会存在一定的偏摆(分解为以三球销球头中心为中点、绕Z轴的偏摆和以三球销球头中心为中点、绕X轴的偏摆),从而产生一定的轴向摩擦力。
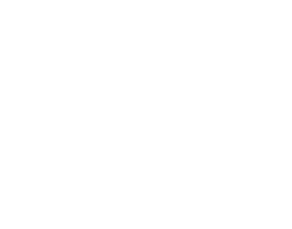
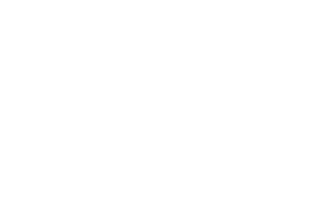
三柱槽壳转一周,球环在滑槽轨道内滑进和滑出完成一个周期的运动。在球环滑移的过程中,存在着滑动摩擦和滚动摩擦,两者共同作用使球环在滑槽内运动。球环与滑槽接触点处的摩擦分析如图2-1 所示,力和力矩关系图如图2-2所示,在三销架轴线与三柱槽壳轴线间存在一定的摆角时,随着万向节的转动,球环在滑槽上滑进和滑出。球环在滑槽上除了沿着销轴轴线方向的滑动摩擦外,还存在绕着销轴轴线的滚动摩擦。滑动摩擦沿着销轴的轴线方向,使球环沿着销轴做轴向滑动;滚动摩擦垂直于销轴的轴线方向,使球环绕着销轴的轴线滚动,滚动摩擦是由球环与销轴之间的偏转扭矩所引起的;球环在滑槽上受的总的滑移摩擦力沿着滑槽的轴线方向。其中,滑动摩擦力是引起球环在销轴上轴向滑移的最主要原因。球环在滑槽上既有滑动摩擦,又有滚动摩擦,对于球环1来说,在滑槽轴线方向上球环1所受的滑动摩擦和滚动摩擦分别为[8]:
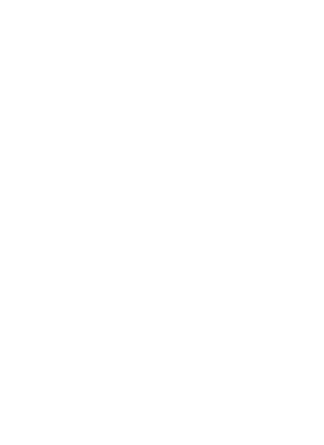
球环所受摩擦力是三球销式万向节产生轴向力F的直接原因[8],球环1在滑槽上所产生的轴向力F1可以表示为:
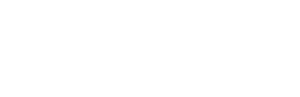
由于三个球环之间的夹角均为2/3π,那么球环2、球环3在滑槽上所产生的轴向力F2、F3分别为[8]:
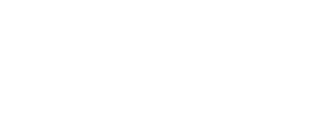
三个球环在滑槽上产生的轴向力分别为F1、F2、F3,方向均沿着滑槽的轴线方向,F1、F2、F3共同作用使得万向节产生一总的轴向力F,
当转角ψ=30°、90°、150°、210°、270°、330°时,总的轴向力F取得最大值。轴向力F随转角变化规律见图2-3。
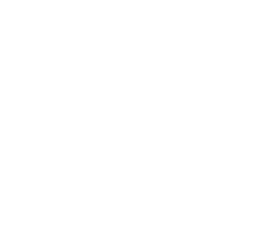
(三)三销架球头与滚针轴承内圈内表面之间的滑动摩擦力,其轴向分力为F3。三销架轴销有效臂长越接近球环圆弧中心高度,接触力越小。在三柱槽壳转动的过程中,球环与销轴间存在沿着销轴轴线方向的滑动摩擦,也存在绕销轴轴线的滚动摩擦。其中,滑动摩擦使得球环沿着销轴轴线上下移动,球环中心到三销架中心的距离也会变化,三个球环在三个销轴上产生的滑动摩擦力共同作用于三销架,给三销架一个径向作用力,其方向垂直于三销架的轴线。此径向力也使得在万向节转动时,三销架产生一个径向振动。三个球环沿着销轴轴线的滑动摩擦分别为:
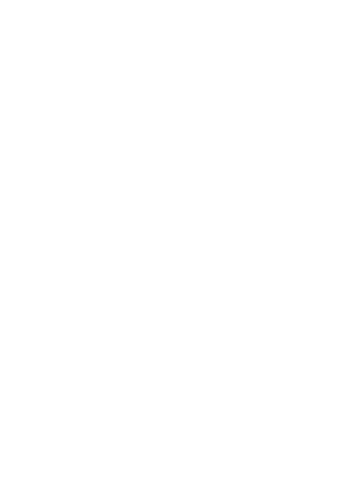
未优化的ARR结构,0°摆角条件下,三销架轴销有效臂长与球环圆弧中心一致,当轴杆和三柱槽壳摆角逐渐增加后,三销架轴销有效臂长与球环圆弧中心距离差值也逐渐变大,接触力在此过程中是持续增加的,相应的F=u滑动 ×P× cos Yy中的u滑动 ×P也是持续增大,( cosYy为摩擦力投影到轴线方向的转换,Yy为三销架轴颈线相对于三柱槽壳中轴线的夹角),为降低该方向的摩擦力,优化后的AAR结构,0°摆角条件下,三销架轴销有效臂长与球环圆弧中心高度不一致,当轴杆和三柱槽壳摆角逐渐增加后,三销架轴销有效臂长与球环圆弧中心高度差值逐渐变小至0后再逐渐变大,接触力及相应的u滑动×P 再此过程中会先减小后增加;即优化后的摩擦力可以视为和优化前的摩擦力存在一定的摆角差。另外, F3与u滑动 ×P成比例关系,也可以通过降低u滑动滑动摩擦系数来减小F3,如提高球环表面和滚道表面粗糙度精度,使用低摩擦系数油脂等方案。
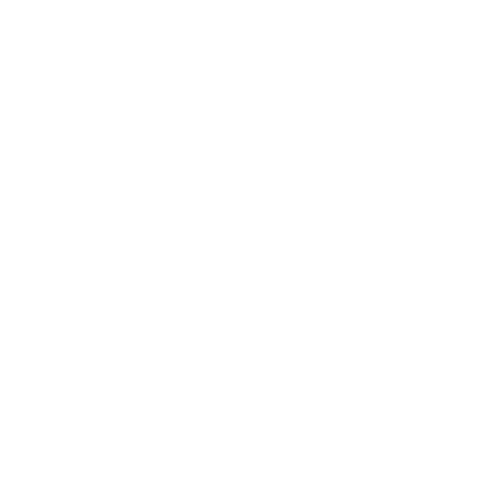
4.摩擦力影响因素对比分析
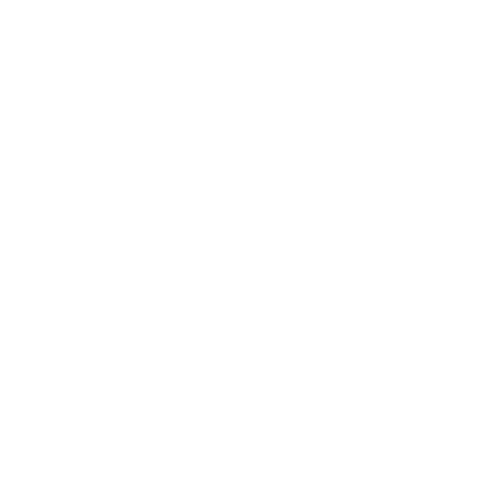
影响摩擦力主要由四个方面的因素:滚针轴承灵活性、三销架轴销有效臂长与球环圆弧中心高、润滑脂摩擦系数和零件表面粗造度。见下表3-1
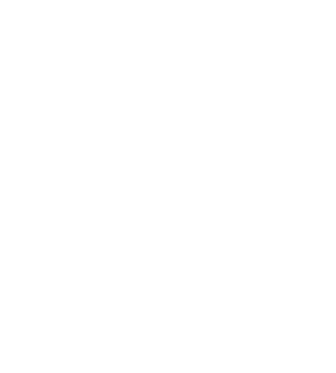
实际生产中,方案1和2在大批量生产时比较容易实现,实现周期比较短,成本低。改善后的轴向派生力测试结果(单位N)见表2,可满足技术要求。
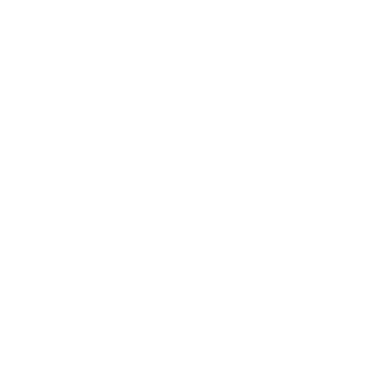
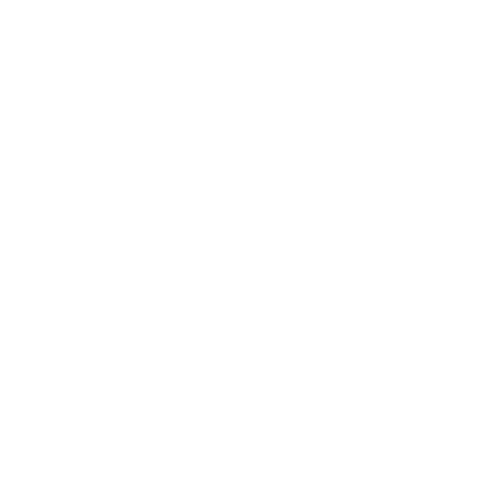
5.结束语
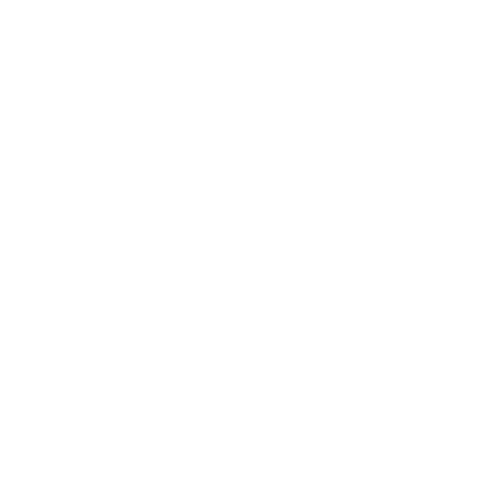
5.1驱动轴可轴向移动的万向节带角度转动时,内部零件之间的相对运动会产生摩擦力,一般可通过提高内部滚针轴承的灵活性、采用低摩擦系数的润滑脂和提高零件表面粗糙度来降低摩擦力,以降低传动轴内部噪音。5.2零件之间的相对滑动产生的轴向分力即轴向派生力,主要影响因素为三销球节运动轨迹和球道中心圆的偏移量,在滚针轴承灵活性和润滑脂摩擦系数已优化的前提下,一般采用优化球道中心圆尺寸减小中心园偏移量来优化球节运动摩擦轨迹,如球道中心圆由圆形改为椭圆形,降低轴节与球笼滑轨之间的摩擦阻力。5.3通过优化球道中心圆尺寸来减小摩擦噪音,投入成本较低,在实际生产中更容易实现。
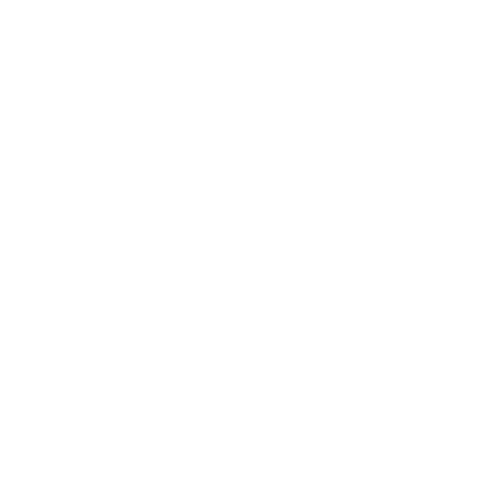
参考文献
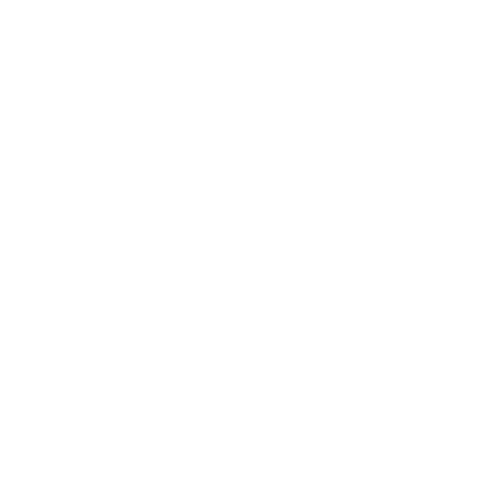
[1] Serveto S, Mariot JP, Diaby M. Modelling and measuring the axial force generated by tripod joint of automotive drive-shaft [J]. Multibody System Dynamics, 2008, 19(3):209-226.
[2] Watanabe K, Kawakatsu T, Nakao S. Kinematic and static analyses of tripod constant velocity joints of the spherical end spider type [J]. ASME Journal of Mechanical Design, 2005, 127(6):229-230.
[3] Lim YH, Song ME, Lee WH, et al. Multibody dynamics analysis of the drive shaft coupling of the ball and tripod types of constant velocity joints [J]. Multibody System Dynamics, 2009, 22(2):145-162.
[4]Lee C H,Polycarpou A A. A phenomenological friction model of tripod constant velocity(CV)joints[J]. Tri⁃bology International,2010,43(4):844-858
[5] Lee K H,Lee D W,Chung J H,et al. Design of generated axial force measurement tester for tripod constant velocity joints under shudder condition[J]. Journal of Mechanical Science & Technology,2014,28(10):4005-4010.
[6]Sa J S,Kang T W,Kim C M. Experimental study of the characteristics of idle vibrations that result from axial forces and the spider positions of constant velocity joints[J]. International Journal of Automotive Technology,2010,11(3):355-361.
[7]Serveto S,Mariot J P,Diaby M. Modelling and measuring the axial force generated by tripod joint of auto⁃motive drive-shaft[J]. Multibody System Dynamics,2008,19(3):209-226.
[8]张杰,张敏中.三销式等速万向节的受力分析[J].江苏理工大学学报:自然科学版,1998,19(5):101-105.
注:文章中引用数据和图片来源网络